SPS(Spark Plasma Sintering,放电等离子烧结)是一种新型的材料烧结技术,通过脉冲电流产生的等离子体活化、焦耳热效应及压力作用,实现材料的快速致密化烧结。其烧结机制和高效性使其在金属、陶瓷、复合材料等领域展现出显著优势。以下从原理及应用两方面展开分析:
SPS烧结的核心是通过脉冲电流和机械压力协同作用,激活颗粒表面并快速传递热量,从而在较低温度和短时间内完成致密化烧结。其工作原理可分为以下几个关键环节:
(1)脉冲电流的等离子体活化效应
SPS烧结过程中,直流脉冲电流通过模具和待烧结粉末颗粒。由于粉末颗粒间存在微小间隙(类似微型电容器),脉冲电流瞬间通过时会在颗粒间隙产生微区等离子体放电(非传统意义上的高温等离子体,而是局部瞬态放电现象)。这种放电会产生以下作用:
- 颗粒表面活化:放电产生的高能电子轰击颗粒表面,清除吸附气体(如氧化物、水分)、杂质或弱结合层,暴露出新鲜活性界面,增强颗粒间的扩散能力;
- 局部加热:放电瞬间的高温(可达数千摄氏度)使颗粒表面快速升温,形成局部“热点”,加速原子迁移。
(2)焦耳热效应的快速升温
脉冲电流通过导电模具和粉末颗粒时,因电阻产生焦耳热(Q = I^2Rt
)。由于粉末颗粒的比表面积大、电阻率高,电流优先在颗粒间通过,导致颗粒自身快速发热(而非依赖外部热源传导),实现从颗粒内部向外的均匀升温。这种加热方式比传统烧结(依赖模具传导热量)效率更高,可在几分钟内达到1000-2000℃的高温。
(3)机械压力的致密化驱动
在烧结过程中,SPS设备通过液压系统对模具施加轴向压力(通常为几十至几百MPa)。压力作用主要体现在两方面:
- 颗粒重排:初始松散粉末在压力下发生颗粒重排,填充孔隙,初步降低孔隙率;
- 塑性变形与扩散结合:高温下颗粒因压力发生塑性变形,原子扩散(表面扩散、晶界扩散)加速,促进颗粒间的冶金结合,实现快速致密化。
(4)综合协同效应
SPS在于脉冲电流、焦耳热和压力的协同作用:脉冲放电活化颗粒表面,降低扩散势垒;焦耳热实现快速升温,缩短烧结时间;压力驱动颗粒重排和塑性变形。三者共同作用,使材料在较低温度(比传统烧结低200-300℃)、短时间内(传统烧结需数小时,SPS仅需几分钟至几十分钟)达到高致密度(相对密度>95%),同时抑制晶粒异常长大,保留纳米结构或微观组织特征。
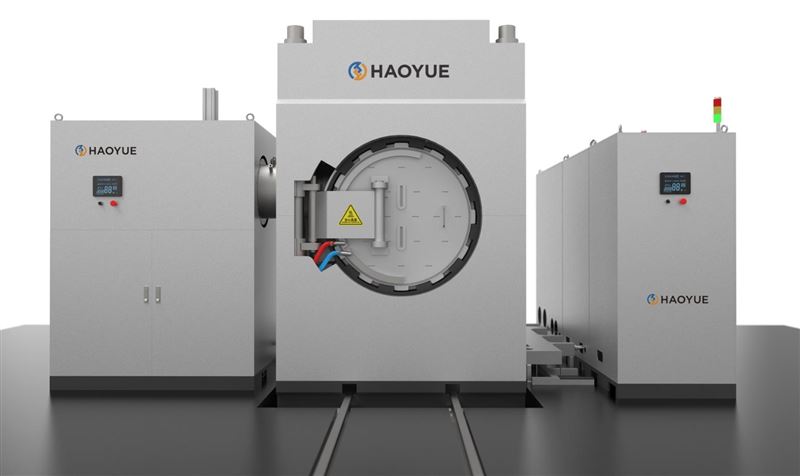
二、SPS在材料烧结中的应用
SPS技术的快速升温、低温烧结和晶粒细化特性,使其在金属、陶瓷、复合材料等领域具有广泛应用,尤其适用于对烧结温度敏感、需保留纳米结构或制备梯度功能材料的场景。
(1)金属及合金材料
- 难熔金属与合金:如钨(W)、钼(Mo)等难熔金属因熔点高、传统烧结需高温长时间,易导致晶粒粗化。SPS通过快速致密化可在较低温度(如1200-1400℃)下实现高致密度,抑制晶粒长大,提升力学性能(如抗拉强度提高20%-30%)。
- 高熵合金:这类新型合金成分复杂,传统烧结易出现成分偏析。SPS的快速升温可减少元素扩散时间,抑制偏析,制备出成分均匀、组织细化的块体材料。
(2)陶瓷材料
- 结构陶瓷:如氧化铝(Al₂O₃)、氮化硅(Si₃N₄)等传统陶瓷,SPS可在1400-1600℃(比传统烧结低200-300℃)下实现高致密度(>98%),减少晶界缺陷,提升断裂韧性(如Si₃N₄的抗弯强度可达1000MPa以上)。
- 功能陶瓷:如钛酸钡(BaTiO₃)等压电陶瓷,SPS能抑制晶粒异常长大,保留纳米晶结构,从而优化压电性能(如介电常数提高10%-20%)。
(3)复合材料
- 金属基复合材料:如铝基碳纳米管(CNTs/Al)、铜基石墨烯(Gr/Cu)复合材料,SPS的快速烧结可避免CNTs/Gr在高温下的结构损伤,实现均匀分散与良好界面结合,提升复合材料的导电性、导热性和力学性能。
- 陶瓷基复合材料:如碳纤维增强碳化硅(Cf/SiC)、碳化硅纤维增强铝(SiCf/Al),SPS可在较低温度下完成界面反应控制,避免纤维损伤,制备出高性能复合材料。
(4)梯度功能材料(FGM)
FGM需在同一烧结过程中实现成分与性能的梯度分布(如热障涂层中从金属到陶瓷的渐变)。SPS通过分区加热和压力控制,可精确调控不同区域的烧结参数(如温度、压力、时间),实现成分与微观结构的连续梯度过渡,满足航空航天等领域对耐高温、抗热震材料的需求。
(5)生物材料
- 多孔生物陶瓷:如羟基磷灰石(HA)支架,SPS可通过调节压力和脉冲参数控制孔隙结构(孔径100-500μm),制备出高孔隙率(>60%)、高力学强度的支架,满足骨组织工程对生物活性和力学支撑的双重要求。
- 金属植入体:如钛合金(Ti-6Al-4V)植入体,SPS的低温快速烧结可减少晶粒粗化,提升疲劳寿命,同时表面活化效应有助于后续生物涂层(如羟基磷灰石涂层)的结合强度提升。
三、SPS技术的优势与挑战
(1)优势
- 快速高效:烧结时间短(几分钟至几十分钟),能耗低(比传统烧结节能30%-50%);
- 低温致密化:降低晶粒长大倾向,保留纳米结构或微观组织特征;
- 组织可控:通过调节脉冲参数(频率、电压)、压力和温度曲线,精确控制孔隙率、晶粒尺寸和界面结合;
- 广泛适用性:适用于导电性材料(金属、导电陶瓷)及部分非导电材料(需模具导电)。
(2)挑战
- 设备成本高:SPS设备需高压电源、精密液压系统和耐高温模具,初期投资大;
- 非导电材料限制:对非导电材料(如氧化铝陶瓷原始粉末)需添加导电添加剂(如碳粉)或采用复合模具;
- 工艺参数优化复杂:脉冲参数、压力、升温速率等需针对不同材料体系反复试验,工艺窗口较窄。
总结
SPS烧结技术通过脉冲电流活化、焦耳热快速升温及机械压力协同作用,实现了材料的低温快速致密化烧结,在金属、陶瓷、复合材料等领域展现出显著优势。随着设备小型化、工艺智能化及成本降低,SPS有望在装备制造、新能源材料、生物材料等领域进一步推广,成为材料制备领域的重要技术之一。